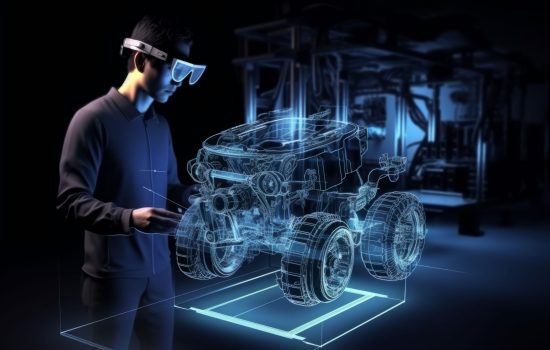
Introduction
- One of the big Indian brands of worldwide automobile industry.
- They want to increase productivity due to increasing demand.s of worldwide automobile industry.
- Along with more efficiency
- Have different sources and different locations of supply of car body.
Client Background
- This automobile manufacturing company had been facing challenges related to production efficiency.
- This company is leading car manufacturing leader in market
- Car production capacity near about 500-600 per day from current location.
Problem Statement
- High labor costs
- Car Body handling and movement from one position to another
- Production bottlenecks
- Production dependency on supply of car body from outsource
- There was no buffer for production plan
- Quality control issues
- Sorting of car body as per Market, Color, Export, Model types
Objectives
- Increased production efficiency
- Car Body handling and movement from one position to another
- Reduction in labor costs
- Improved product quality
- Enhanced safety measures
- Sorting of car body as per Market, Color, Export, Model types, etc.
Solution Implemented
- Solution implemented to address the identified challenges, including:
- Conveyors for movement of car body, Rack systems to storage of car body.
- In Three different sections.
- Four Stackers for material handling
Implementation Process
- Planning and design phase step wise
- Civil work
- Rack installation, Stacker installation and PLC programming for all stacker
- Stage wise WMS Programming for all four stackers
- In Welded Body Shop (WBS), Painted Body Shop(PBS), Special Car Body Section, and Specific car body pickup point for inward from outsources locations.
- JIT integration
- Role base module as per employment category
- Testing and optimization of systems
- Training for employees department wise
Results and Impact
- Quantitative and qualitative analysis of the results achieved post-ASRS, such as:
- Increase in production output
- Reduction in labor costs
- Improvement in product quality metrics, due to
- Resolution of time body availability
- Proper and timely sorting as per Market, Color, Export, Model types, etc.
- Reduced body handling.
- Lesser damages in transit and in production.
- Eliminated dependency of outsourced supply of car
- Increased buffer stock by 75%
- Enhanced employee safety
- Improved customer satisfaction levels
Key Success Factors
- Key factors contributing to the success of the ASRS project, include
- Selection of appropriate automation technologies
- Successful reduction / management of labor costs
- Car Body handling and movement from one position to another
- Production bottlenecks resolved
- Sorting of car body as per Market, Color, Export, Model types
- Employee training and engagement
- Continuous monitoring and optimization of ASRS systems
- Operations from any location of factory
- Role base operation facility
- JIT base sorting of car body
Lessons Learned
- Reflection on the lessons learned from the ASRS project:
- Importance of thorough planning and preparation
- In-depth understanding of client processes and ground reality
- Flexibility to adapt to changing requirements
- Continuous improvement mindset
- Value of investing in employee training and development
Conclusion
- Production bottlenecks resolved
- Higher production achieved with reduction in labor costs
- Improvement in product quality delivered
- Enhanced employee safety achieved