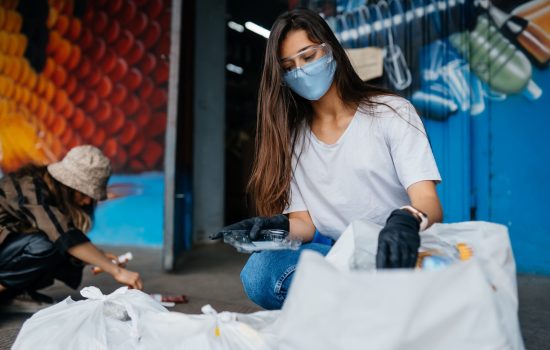
Introduction
- One of the big Indian brands of industry for Industrial Hazardous and Non Hazardous Wastes Recycling.
- They wanted to increase productivity due to increasing demand for Hazardous and Non Hazardous Wastes Recycling.
- They decided to implement ASRS solutions to streamline the production processes.
Client Background
This group is the leader in its industry and has proven its expertise in Industrial Hazardous and Non Hazardous Wastes Recycling through Pre Processing, Industrial Waste Water Recycling through CETP- ZLD facilities and successfully developing sustainable Eco Textile Parks. The group, as part of ‘Swachh Bharat Mission’, is engaged in production of Sustainable Alternate Fuel (SAF) from Municipal wastes.
Problem Statement
- Hazardous working atmosphere
- High labor costs
- Production bottlenecks
- Sorting of material section wise as solid and liquid types for production
- Quality control issues
Objectives
- Client aims to achieve the following through ASRS:
- Increased production efficiency
- Reduction in labor costs
- Improved product quality
- Enhanced safety measures
- Sorting as per solid and liquid types for production
Solution Implemented
- Solution implemented to address the identified challenges, including:
- Conveyors for movement of wastes to their racks as per its nature – hazardous or not.
- Two different sections solid and liquid.
- Stackers for material handling
- Inward section
- Outward section
Implementation Process
- Planning and design phase step wise
- Civil work
- Rack installation, Stacker installation and PLC programming for all stacker
- Stage wise WMS Programming for all two stackers, four inward and outward trolleys.
- Role base module as per employment category
- Testing and optimization of systems
- Training for employees department wise
Results and Impact
- Quantitative and qualitative analysis of the results achieved post-ASRS, such as:
- Increase in production output
- Reduction in hazardous atmosphere work due to automated handling of hazardous waste
- Reduction in labor costs
- Improvement in product quality metrics
- Proper and safe transportation of hazardous waste
- Lower risk of contamination to input processes
- Error free sorting of waste as per category
- Enhanced employee safety
- Customer satisfaction levels
- Sorting as per solid and liquid types for production
Key Success Factors
- Selection of appropriate automation technologies
- Control of high labor costs
- Hazardous material handling and movement from one position to another
- Production bottlenecks resolved
- Sorting as per solid and liquid types for production
- Employee training and engagement
- Continuous monitoring and optimization of ASRS systems
- Operations from any location of factory
- Role base operation facility
Lessons Learned
- Reflection on the lessons learned from the ASRS project, including:
- Importance of thorough planning and preparation as per product category and type
- Importance of thorough understanding of product characteristics for successful automation of logistics processes
- Flexibility to adapt to changing requirements of waste types
- Continuous improvement mindset
- Value of investing in employee training and development
Conclusion
- Realised complex multicategory material management
- Successfully automated both liquid and solid waste transportation inside the facility
- Achieved assigned project parameters, including
- Increased production efficiency
- Reduction in labor costs
- Improved product quality
- Enhanced safety measures
- Sorting as per solid and liquid types for production
- Internally, ATSPL realized the immense utility of ASRS innovation in any industry